The evolution of quality control in modern industries
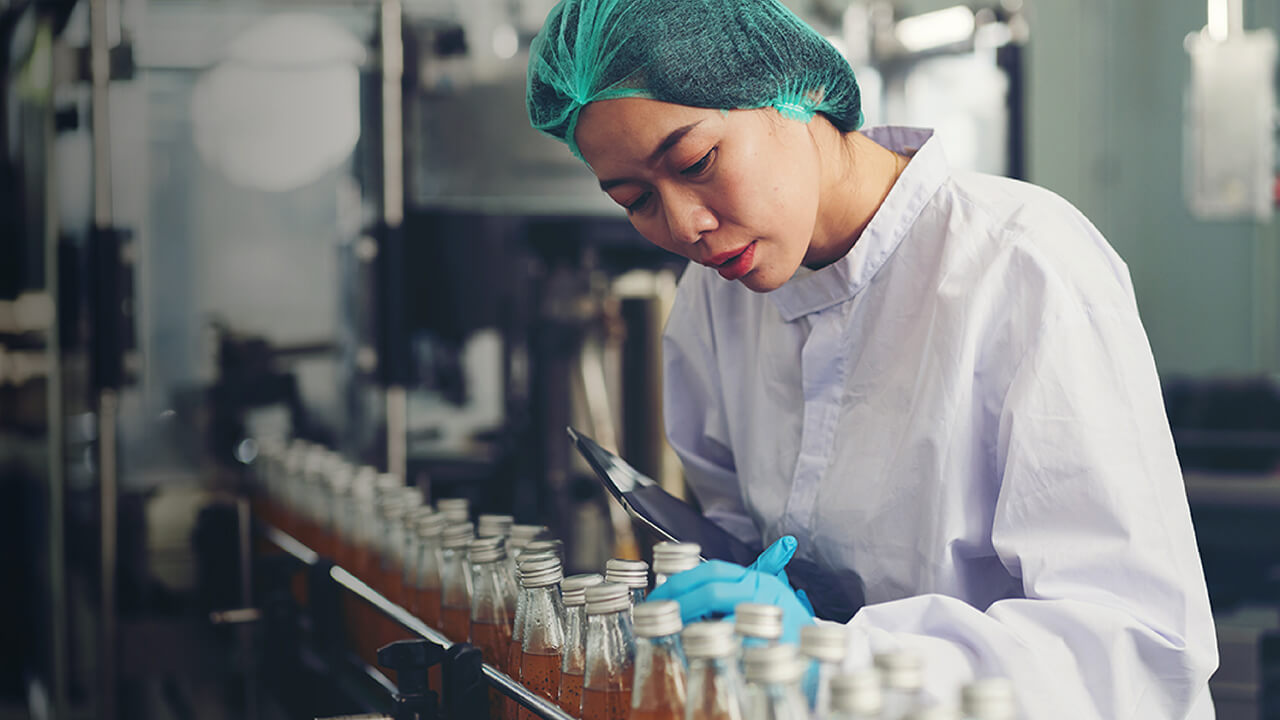
8 min read
Nowadays, quality control seems like it’s been around forever. Considering that the roots of quality control can be traced back to 3000 BC in Babylonia, according to historians, “forever” isn’t so far off.
They may not have had the software tools, processes, and procedures we have today, but the basic principles of improvement have always been essential. These principles led to the invention of the wheel, along with almost every other major advancement known to man. But what exactly is quality control, where did it all start, and how has quality control over the centuries helped us achieve the systems we use today?
What is quality control
Quality control is the process that a business or industry uses to ensure that the quality of products is maintained or, better yet, improved!
Achieving quality control requires the business to create an environment where management and employees strive for excellence. This is achieved by training staff, establishing benchmarks for product quality, and testing products to check for statistically significant deviations.
When did quality control begin?
The concept of quality management has been around since ancient times.
Hammurabi of Babylon, in the 18th century BC, introduced the concept of quality control and liability, establishing legal consequences for builders who did not comply with construction standards. For example, Hammurabi’s Code provided that if a house collapsed and caused the death of the owner, the builder was to be punished with death. This law was an early form of liability and quality management.
During the time of the Egyptian pharaohs, the burial of nobles was systematically recorded. The manner in which the necessary rituals were performed and the grave goods that had to be buried with the deceased are mentioned in each Book of the Dead. Systematic documentation is one of the basic principles of quality management to ensure consistency. The same steps are followed by different people performing the same task. In this way, deviation from requirements can be minimized.
The first emperor of China, Qin Shi Huangdi in the 3rd century BC implemented strict quality control measures, requiring the labeling of all products supplied to the imperial household. This allowed for product traceability and accountability of manufacturers, introducing an early form of control and quality in mass production.
During the Middle Ages, guilds of merchants and craftsmen were established to guarantee the quality of products. Manufacturing standards were set, ensuring that products would meet specific conditions and requirements before reaching buyers.
We can therefore see that from antiquity right up to the Middle Ages, societies adopted various mechanisms to ensure quality, whether through legal frameworks, documentation, or organized guilds. Of course, all of these principles influenced future quality management, shaping the procedures that are applied to this day.
Quality control from the 20th century onwards
And then we come to the industrial revolution, where quality evolved and focused on factory inspections and the removal of defective products. The factory system was based on the skill of workers, with occasional checks to ensure quality.
The industrial revolution began in the United Kingdom in the late 18th century and gradually spread throughout Europe and the rest of the world and managed to introduce the concept of specialization of labor with the division of labor leading to increased productivity. It established the first factories in the United States and Europe, which changed the traditional artisanal model of production and separated craftsmen and shop owners into the new roles of factory workers and production supervisors. The factory system ensured product quality based on the skill of workers, supplemented by occasional checks by production supervisors.
It was not until the early 20th century in the United States that an industrial engineer named Frederick Winslow Taylor developed a new approach to factory management that he called scientific management. Taylor’s scientific management argued that human performance could be defined and controlled through work standards and rules, thereby increasing productivity without increasing the number of skilled workers needed in a factory.
Along with scientific management came minimum complexity and maximum efficiency, which took power away from factory workers and had a largely negative impact on quality.
Although Taylor’s system of scientific management had some flaws, it was a product of its time and developed during a time of mass immigration, when the American labor system was flooded with unskilled, uneducated workers, many of whom lacked advanced English language skills. Taylor believed that his system provided an effective way to employ these workers in large numbers, as well as to reduce conflict and labor disputes in an era of frequent public labor disputes.
From the Industrial Revolution to Modern Quality Management
The approach developed by Frederick Winslow Taylor brought improvements in productivity, but it also created great challenges, as product quality was based mainly on occasional checks and individual worker performance, factors that did not ensure the stability of results.
A few years later, in the 1920s and 1930s, the concept of evaluating production processes to promote product quality entered the American system. Statisticians in Germany and America applied statistical methods to analyze and control quality variations in the product manufacturing process. In 1924, Walter A. Shewhart of Bell Telephone Laboratories developed a statistical chart for controlling product variables in manufacturing, an innovative milestone that is considered the beginning of an approach to quality known as statistical quality control.
The rapid development of quality management systems occurred after World War II, when W. Edwards Deming, a statistical engineer, and Joseph Juran, an expert in quality management, introduced their ideas to Japan.
Japanese manufacturers developed Total Quality Management, emphasizing continuous improvement and the participation of all employees in the quality assurance process.
Soon buyers around the world were demanding Japanese products, making headlines as far away as London and the United States. In 1951, the Japanese established the Deming Prize to honor Deming’s significant contribution to the promotion of quality in the country. The prize remains one of the most important quality management recognitions in the world and continues to fulfill its purpose of promoting quality management in Japanese industry. By 1954, the concept of total quality control (TQC) had been adopted by Japanese management, which had simplified, strengthened, and modified Deming’s ideas for widespread application in manufacturing. Total quality control, as developed by the Japanese, is an effective system for integrating the efforts of various groups in an organization to develop, maintain, and improve quality, to enable economical production and service that create complete customer satisfaction.
By the 1970s, Japan was surpassing the United States in manufacturing cars and electronics. Experts like Juran had predicted this trend, but it still caught many companies by surprise.
For the most part, American companies believed that increased competition from Japan was all about lower prices. As consumers bought Japanese products, American companies began to lose market share, leading to cost-cutting and import-restriction strategies. Not surprisingly, these methods did little to improve the quality of the goods.
With the American economy suffering from its inability to compete on quality, American corporate leaders finally took action. Total Quality Management was born, setting the stage for the flourishing of quality and operational excellence strategies in the United States.
In 1987, the first official version of ISO 9000 was published, leading to slow but steady adoption by American companies, laying the foundation for a global approach to quality management, so that businesses could follow uniform control criteria for quality assurance.
In the 1990s, businesses placed a strong emphasis on continuous improvement and process optimization. With methodologies such as Six Sigma, companies could reduce variance and errors in the production process, and with Lean Manufacturing, they could eliminate waste and improve efficiency.
Quality control in today’s era
Today, quality control does not only refer to physical products, but also to services, technology, and customer experience. The gigantic technological development, digitization, and artificial intelligence have dramatically changed the way in which businesses carry out quality control, as we are offered automated controls, real-time data analysis, and predictive maintenance.
Companies now, through technology and new systems such as ERP, have the ability to analyze huge amounts of data in real time and identify patterns, to immediately predict any errors, and they also have the ability to have traceability, which is very important in modern businesses, at every stage of production, ensuring transparency.
Today, more than ever, sustainability is a very important part of quality management. Businesses do not want to focus only on the quality of their products and services, but also on their environmental and social responsibility, the so-called ESG!
The Future of Quality Control
With the rapid development of technology and quality management, we cannot know the limit of the development of quality control. However, we know how important it is for businesses to focus on continuous innovation, flexibility and customer experience, in order to shape the future of quality.
Every business must understand how quality is the key to its success and sustainability.